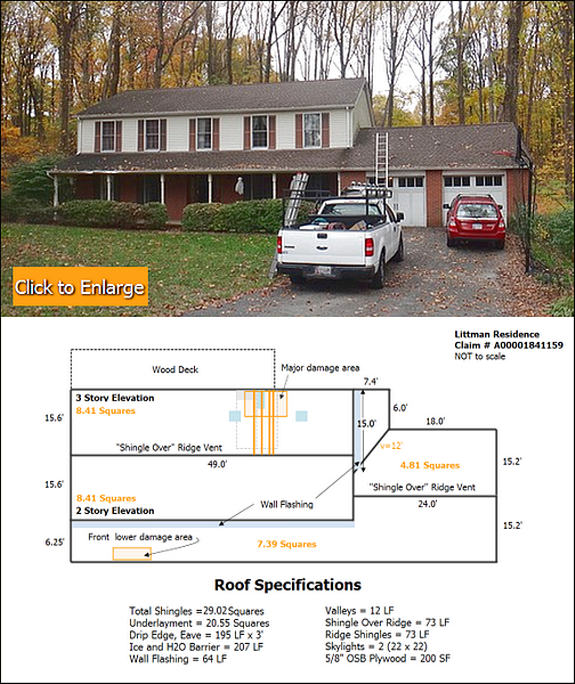 The Littmans in Laurel had their roof assaulted by a large poplar tree in the
weather event shown below.
|
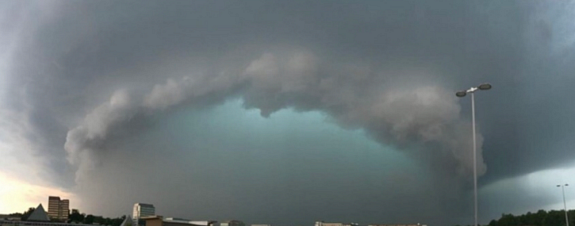 This scary local photo was captured by someone at
the Goddard Space Flight Center in Greenbelt, MD.
|
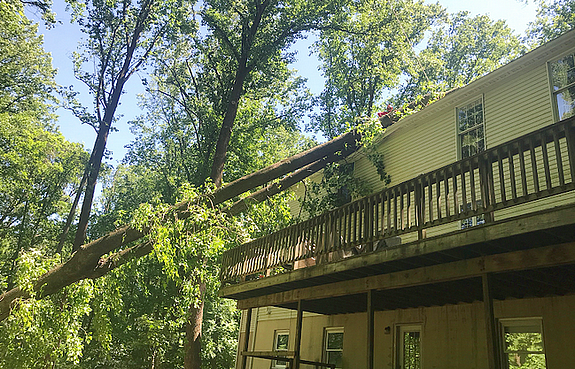 ...and here's the extra large tree that did all of the
damage; it looks to be at least 60 feet tall!
|
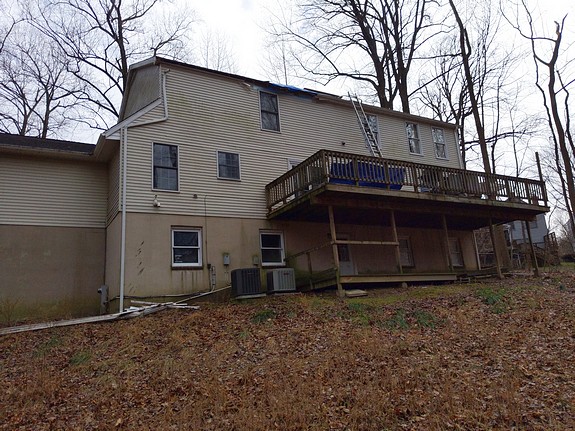
|
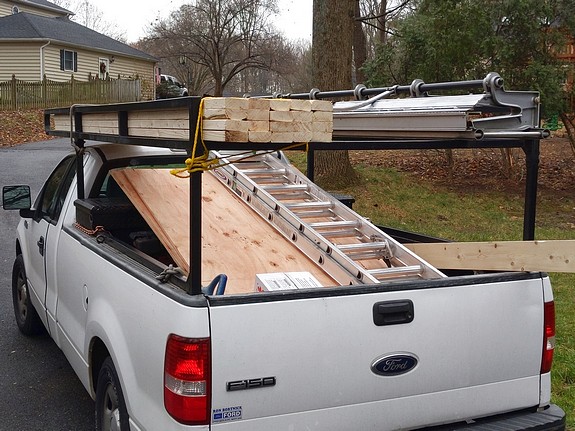 So, with two engineering reports in hand and negotiations
now completed with the insurance company, we're getting ready to begin the rebuilding
process.
|
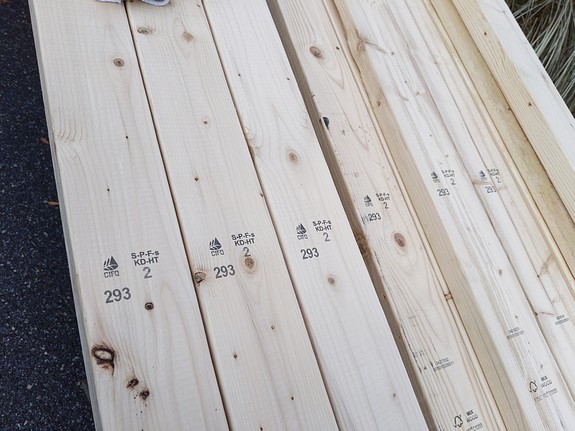 Arriving are #2 SPF hand picked 2 x 4's and CDX plywood as
specified by Vannoy Engineering.
|
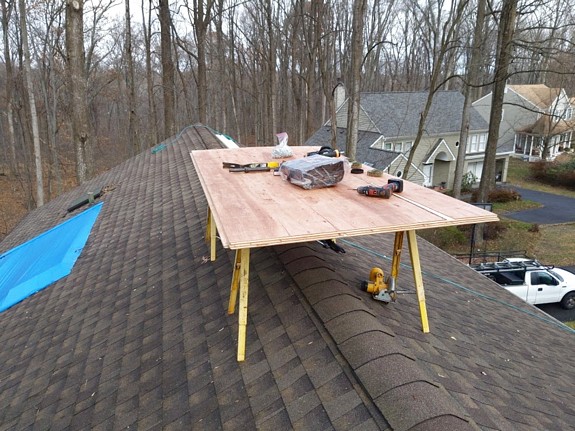
|
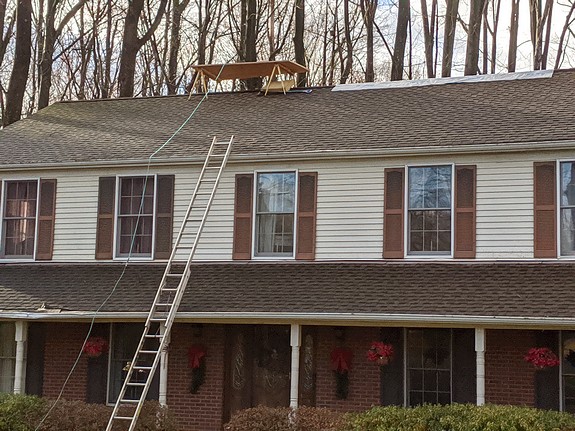
|
 It's time for some forensics... The upper master bathroom
roof was the first location to be hit by the big tree, so we'll start here...
|
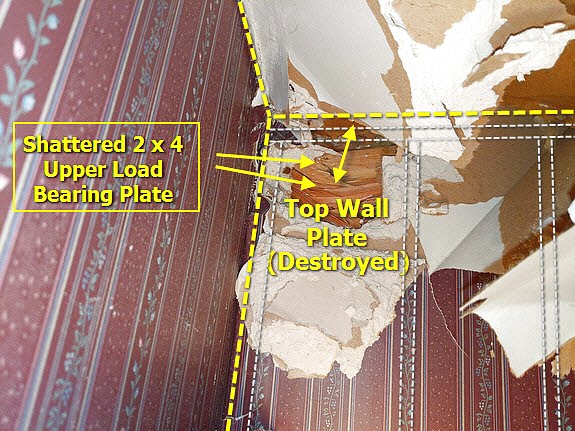 ... and the first thing we noticed was the top of the rear
wall was destroyed. Funny thing, this was totally "missed" by all until we started to actually dig
in.
|
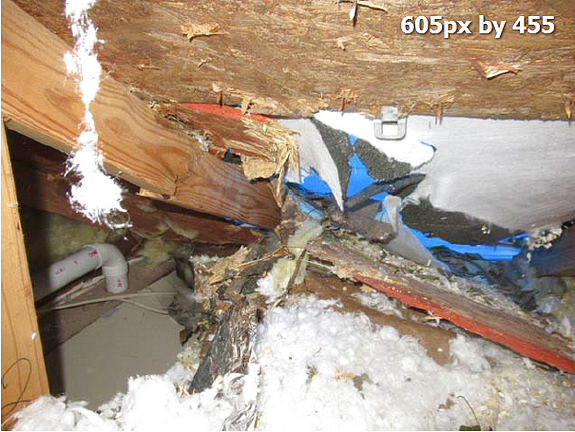 View of damage from inside the attic. It's a
mess.
|
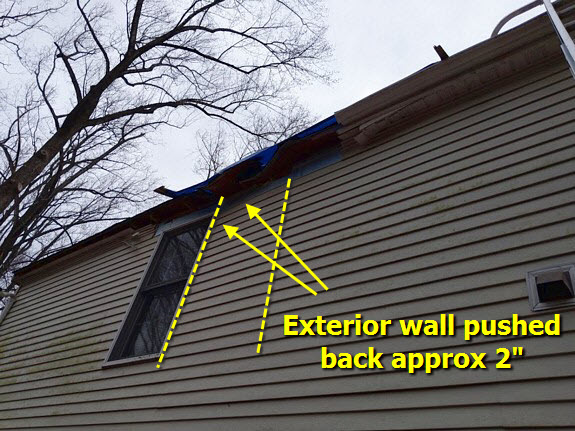 The first part of the construction process was to
completely rebuild about 12 linear feet of the rear wall; it was shoved back about 2" right next
to the window, and of course there was the completely shattered upper plate...
|
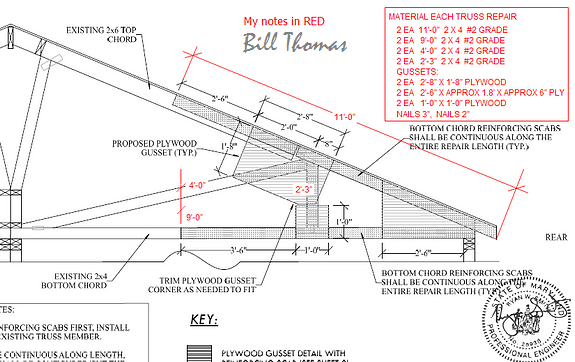 |
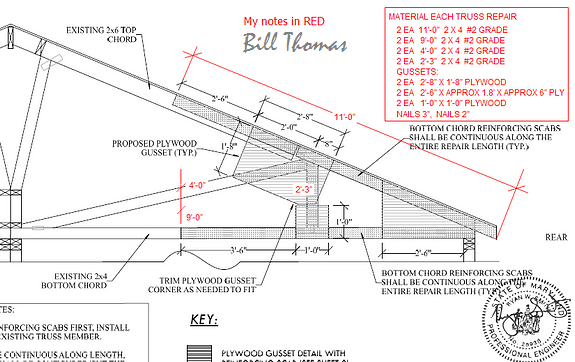
|
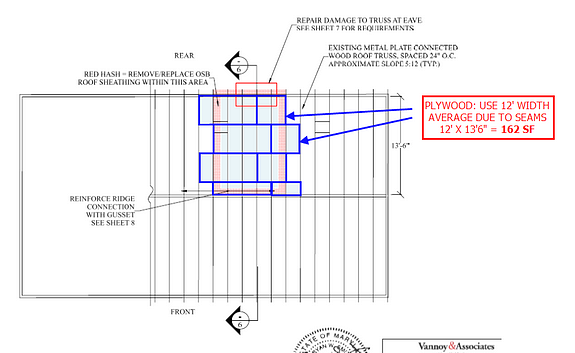 Above are the structural repair drawings provided by the
engineers. We'll comply with their methodology ... leaving the original truss parts in play
and "scabbing" 2 x 4's to them where recommended.
|
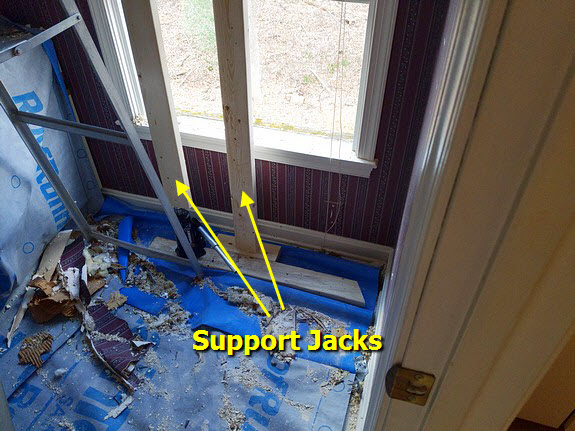 Since at least three trusses were damaged and hanging below
ceiling level, they needed to be raised first -- just a little past their original
position.
|
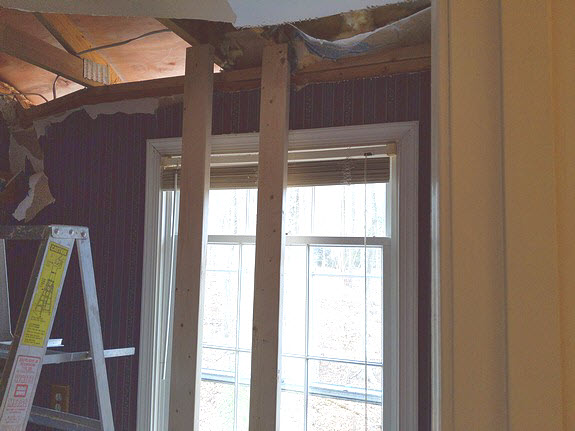 Once successfully raised, we can now continue with our
assessment of the damage.
|
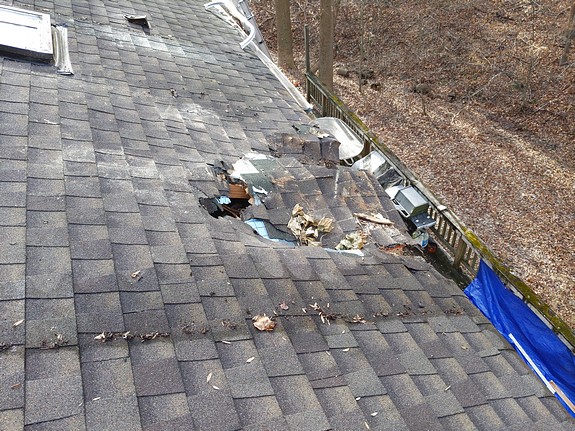
|
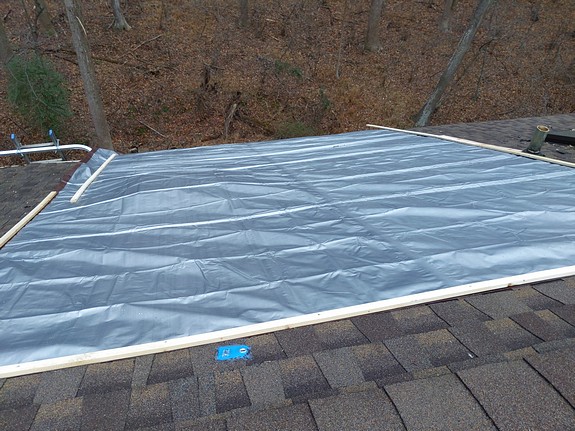 But before more materials were removed, additional
temporary waterproofing was necessary.
|
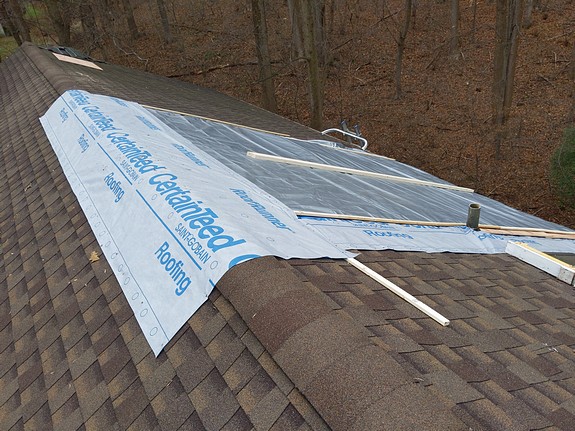
|
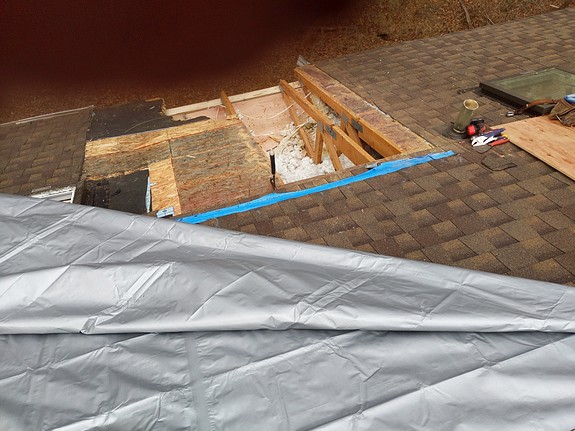
OK, moving ahead and deconstructing the mess we're finding that a few of
the trusses areseverely damaged.
|
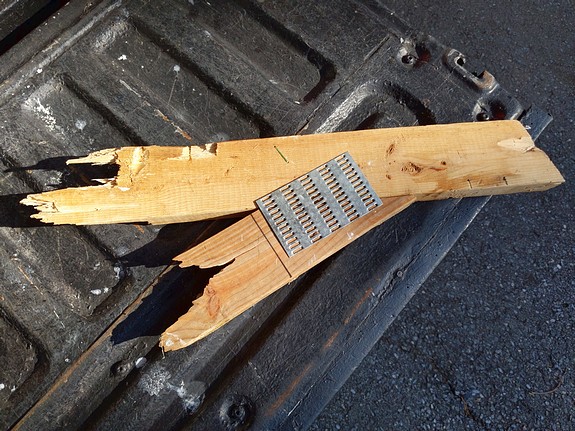 In fact, two of the trusses were in this condition... the
ends completely broken through and barely hanging by a thread. This is the part that actually
supports the entire truss and rests on the exterior wall.
|

|
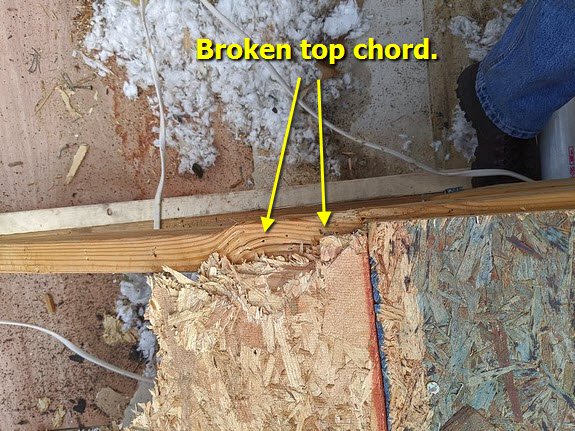 Top chords and support struts were damaged, twisted, and
out-of-position in many places as well.
|
 Unfortunately the previous contractor "overnailed" a few
sections of shingles (causing minor leaks). No problem since we're replacing the entire roof; but
for now only 2 squares of roofing and underlayment are being removed for the local structural
repairs.
|
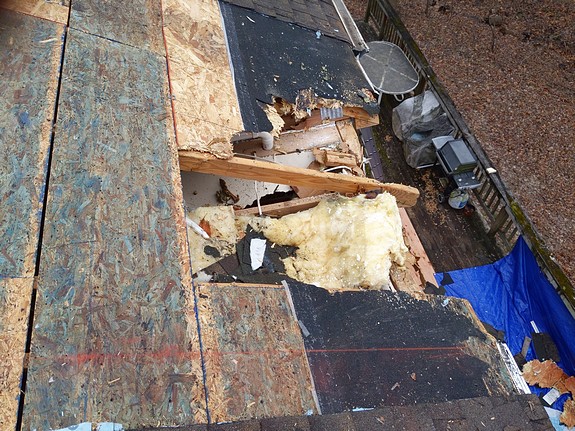
|
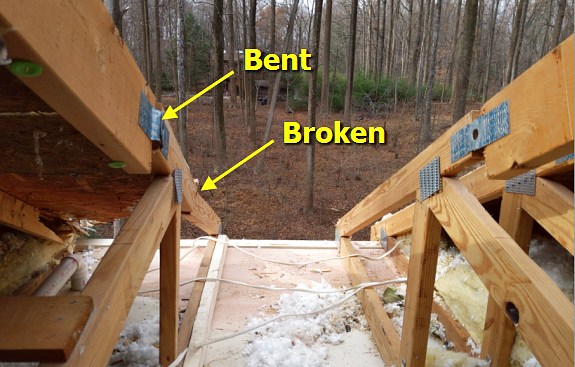
Now that we've
completely inspected the damage, and we know exactly what needs rebuilding, we've moved the
insulation out of the way and are ready to get to work.
And now noting that some of the damage is
serious... we're ready to secure a building permit from the county (as per requirement).
However, it was noted that the original engineer's drawings needed an
upgrade due to newly enacted regulations...
...so the
drawings had to be corrected and re-submitted, and the resulting time lost pushed us past the
Christmas holidays for additional construction...
|
|

|
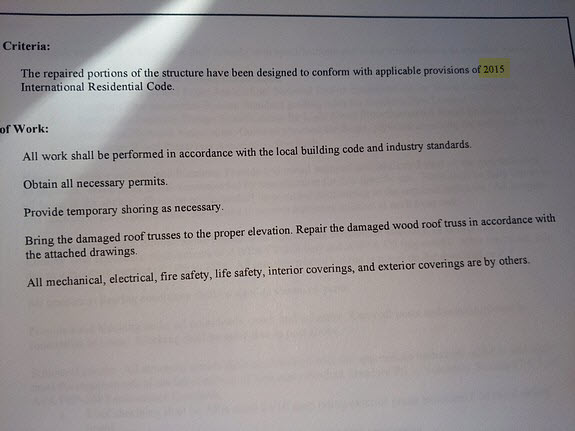
|
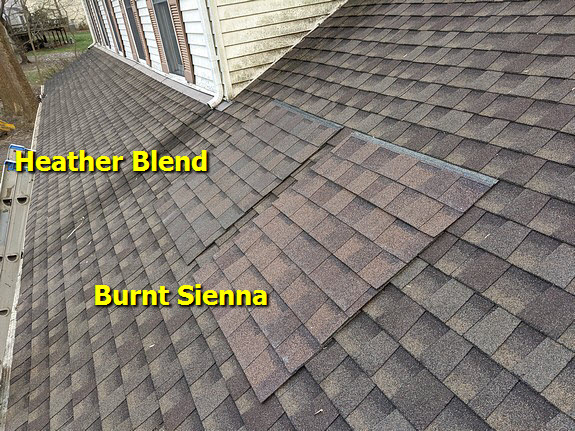
Meanwhile, the Littmans chose a roof color; Heather Blend, very
similar to the original, and perfect for their house.
We finally
acquired the permit and resumed work.
|
 Now the "thing" about repairing broken trusses; it's a
process! Measuring, string lining, tweaking, clamping, re-measuring, calibrating ... is all part
of fitting new materials together with the surrounding construction.
It's time consuming, but worth it; the system will end up much stronger than the original factory
trusses.
|
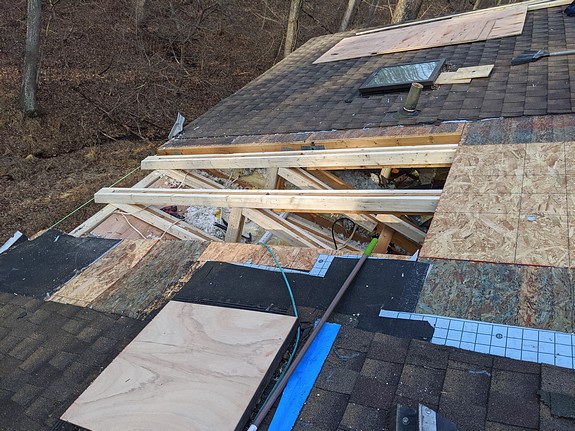 Scabbing the first two trusses here with #10 Common nails
(not sinkers or pneumatic nails) as specified for strength.
|
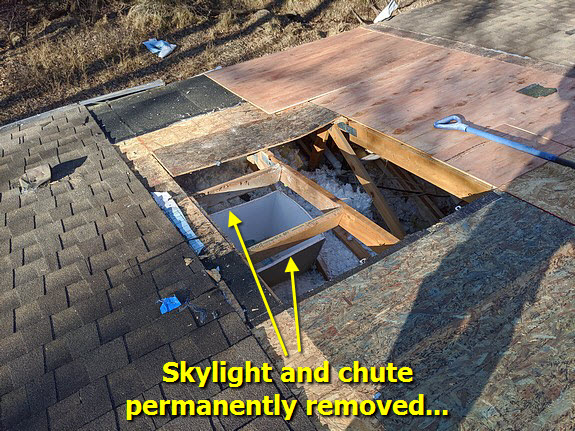 As we progressed it was decided that the skylight
and chute will be eliminated. We also noted that the skylight had been leaking for quite a
while, causing the need to re-frame and replace the plywood in that area...
|
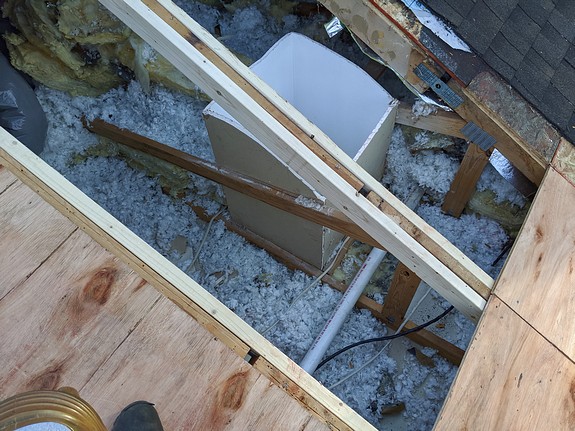 The remainder of the chute will be removed from the
intereior as the bathroom ceiling is replaced
|
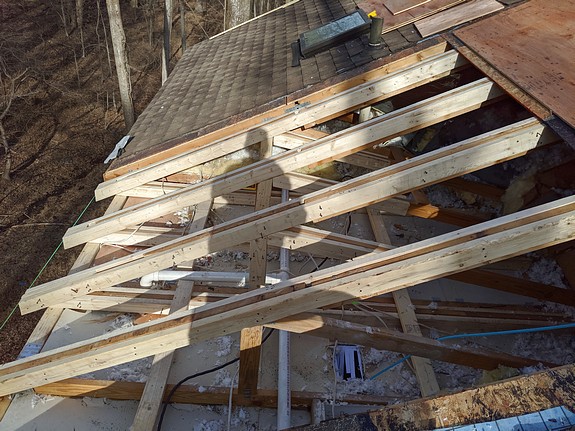 Now all four damaged trusses have been rebuilt, re-leveled
(and plumbed) and are ready for the gussets.
|
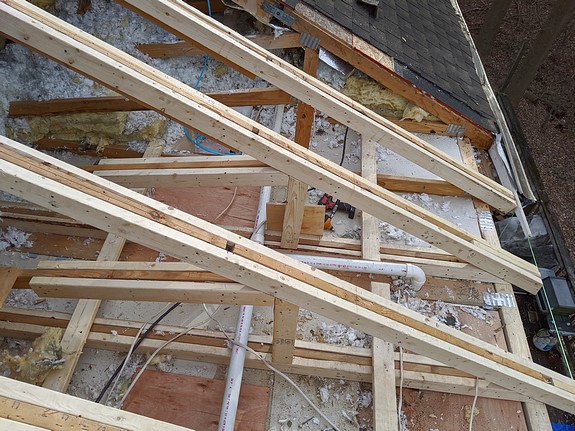 Nice!
|
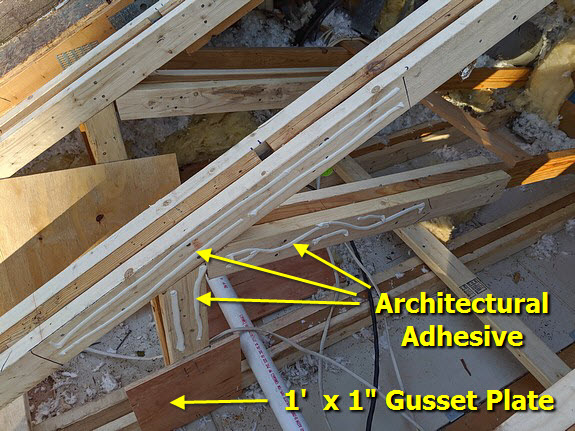 We'll use 1/2" exterior plywood (5 ply for strength!) and
#6 commons (3") for added strength as well.
|
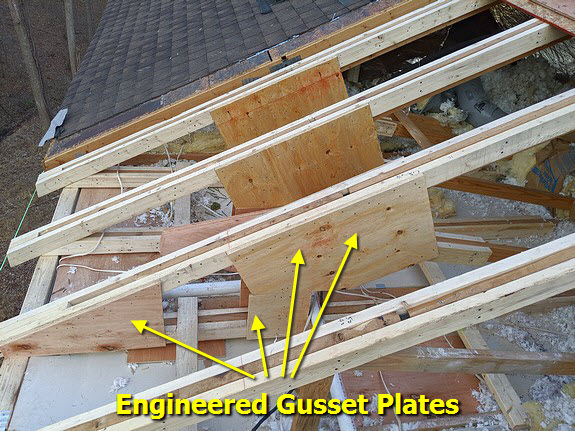 Voila! Almost all trusses are done and ready to
go.
|
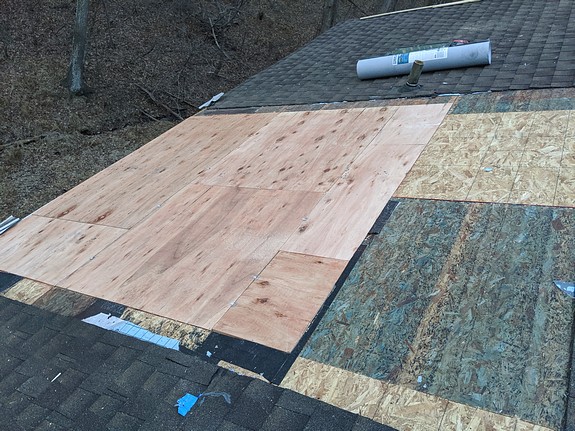 Next, 1/2" CDX 5-ply. Nice!
|
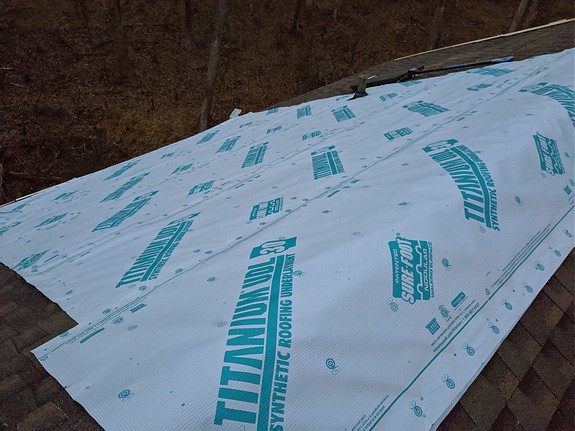
Then Titanium UDL synthetic underlayment (the best!) is permanently
installed, and the area is now completely waterproof once again.
Now we're ready to "change out the
ceiling drywall, and eventually the attic insulation will be moved back into place. Ventilation
issues will be addressed, and a new CertainTeed Landmark Lifetime Architectural Roof will be
installed.
|
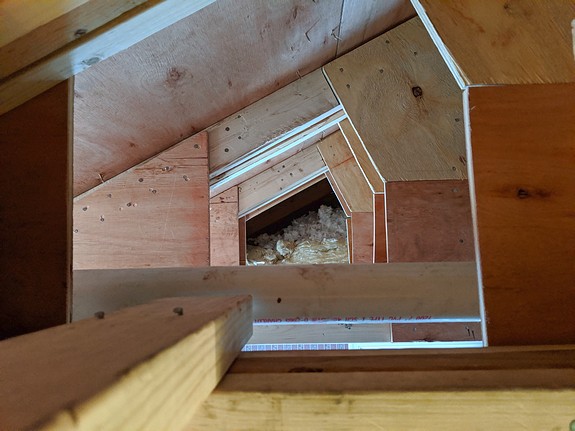
A view of the fancy gussets from the end.
Strong!!
|
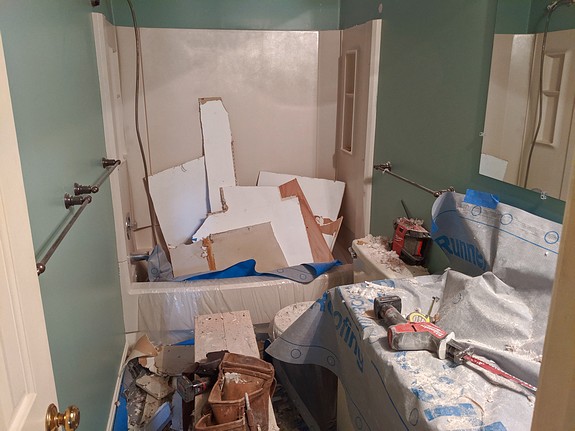
Ceiling drywall removal in the "hall" bathroom.
|
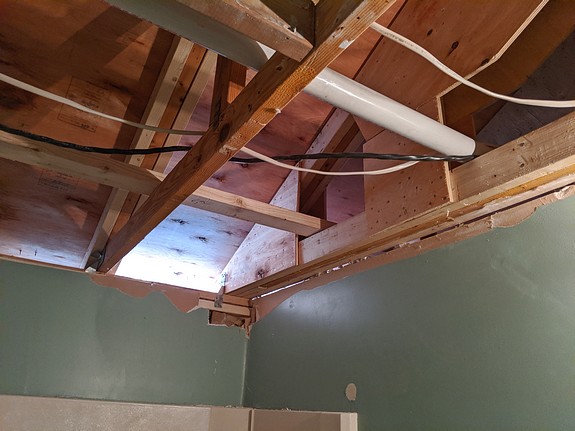
|
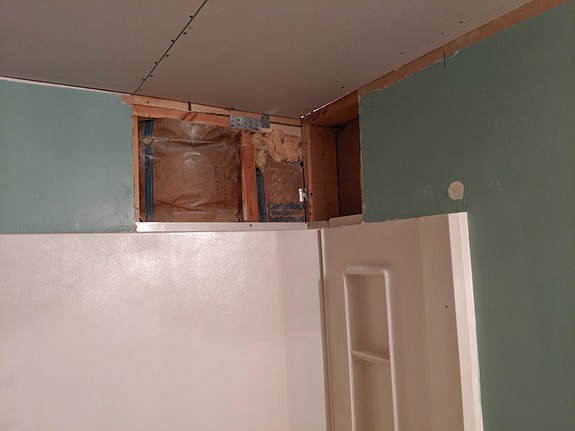
|
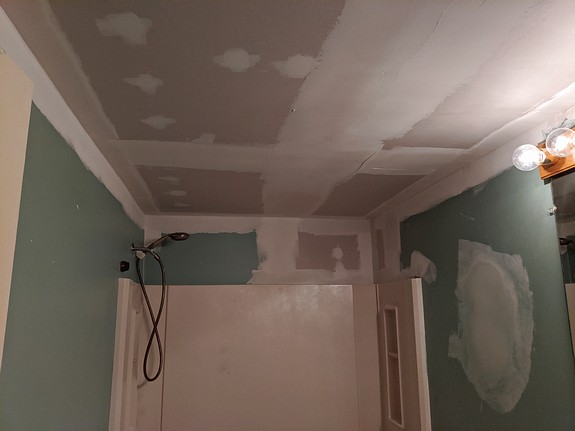
Two coats of compound...
|
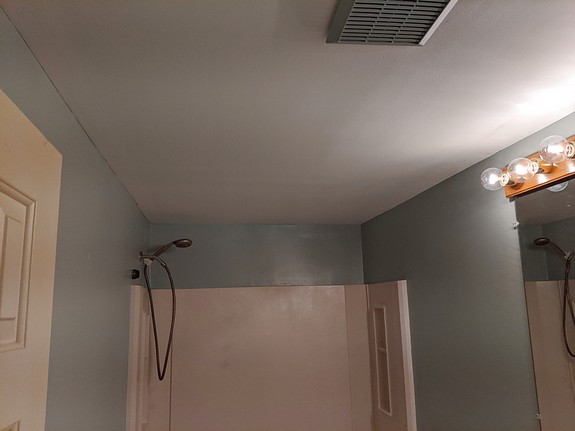
3 coats + wall and ceiling paint (Kilz primer + 2
coats ceiling paint.
|
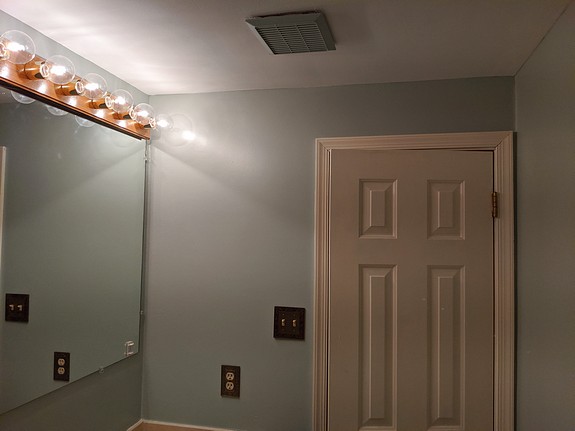
|
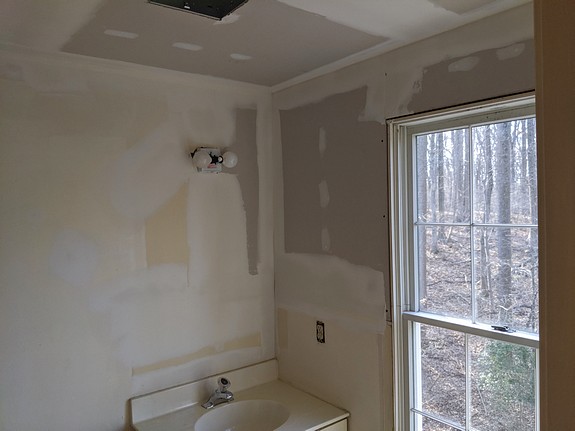
Now for the master bath that was destroyed by the Big
Poplar.
|
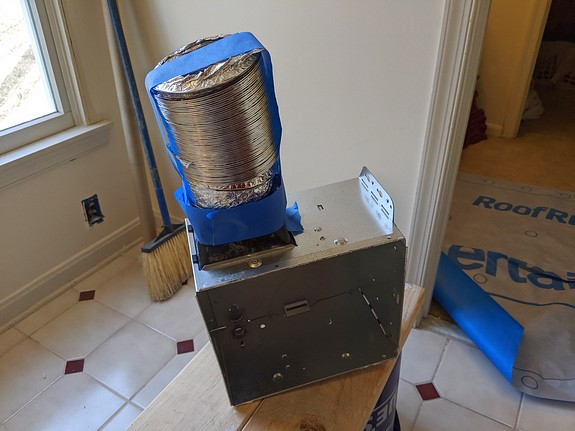
Super fancy ceiling fan, light, and humidistat!!
|
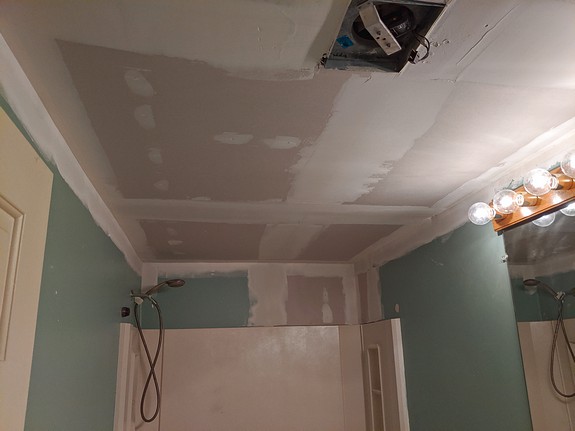
|
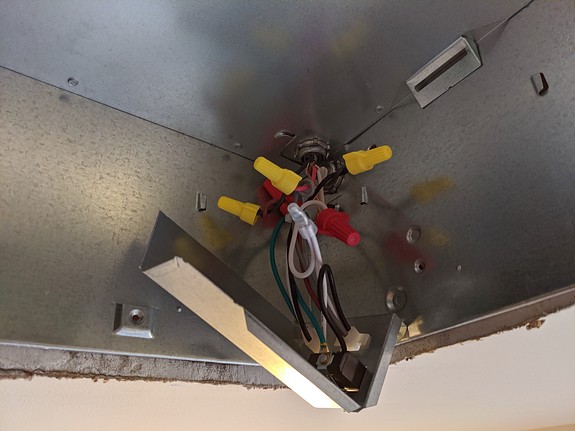
Yep, 3 controls and "five wire."
|
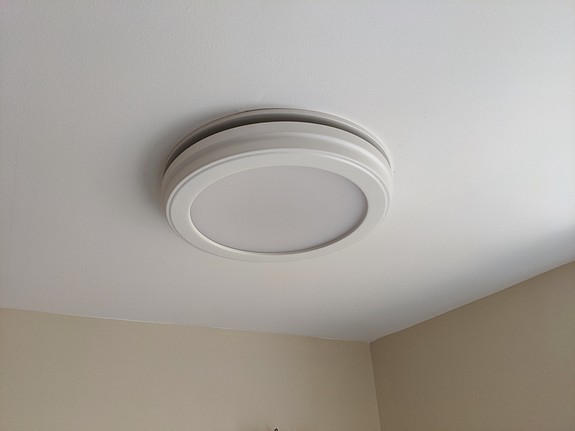
Perfecto.
|
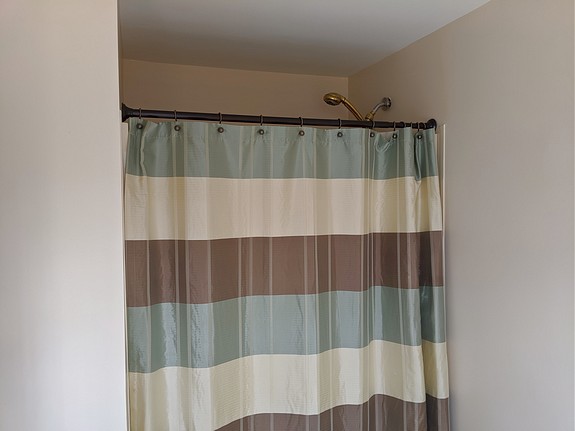
|
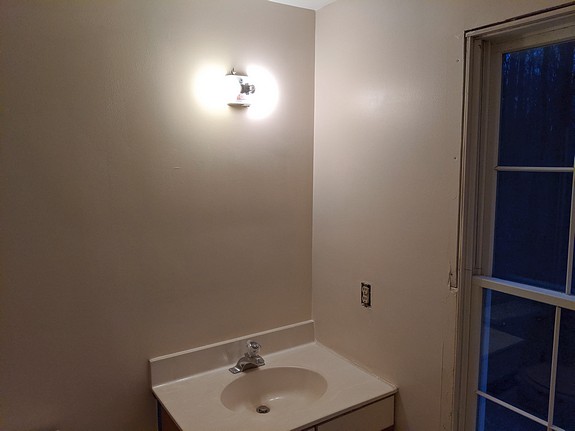
|
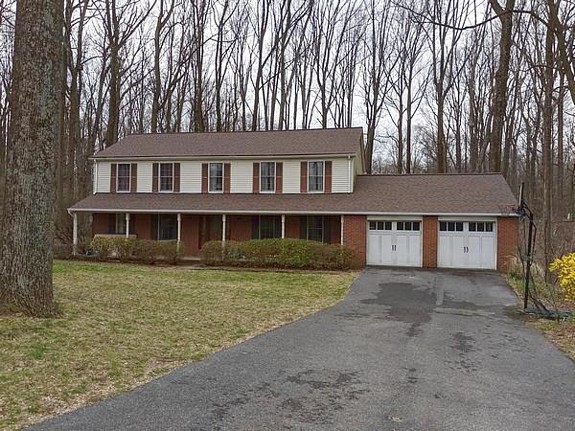
This is the "after" photo of the new CertainTeed
Lifetime Landmark Roof.
|
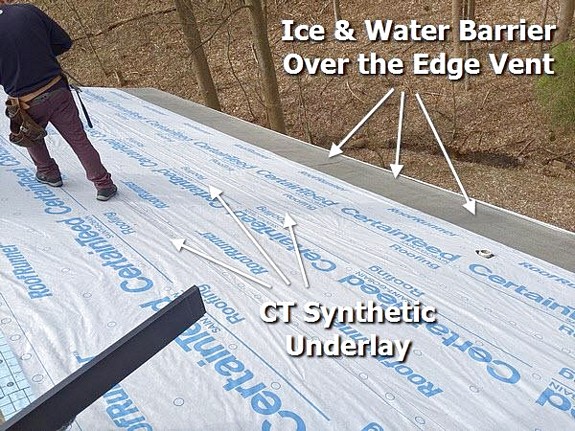
|
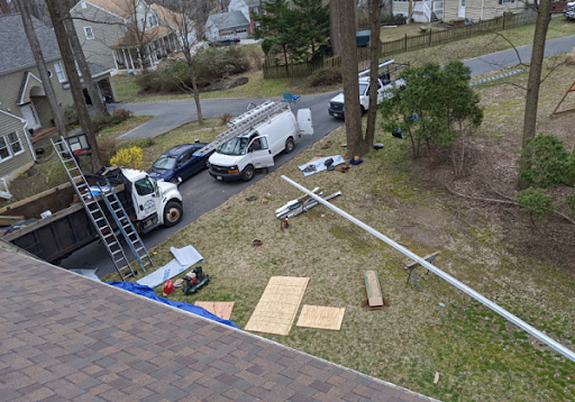
|
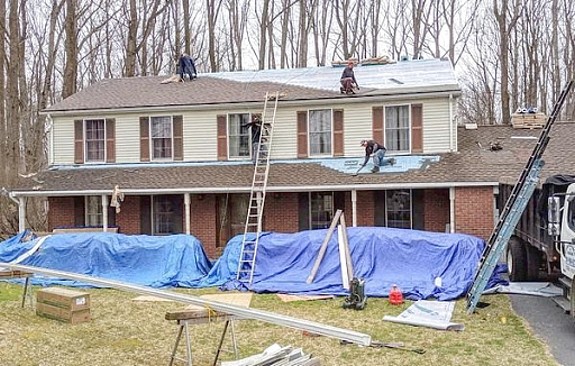
|
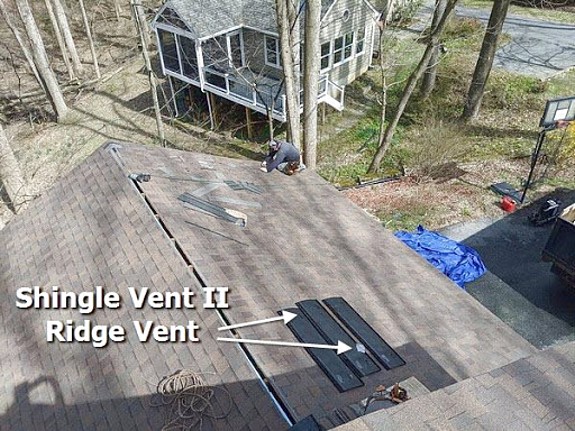
|
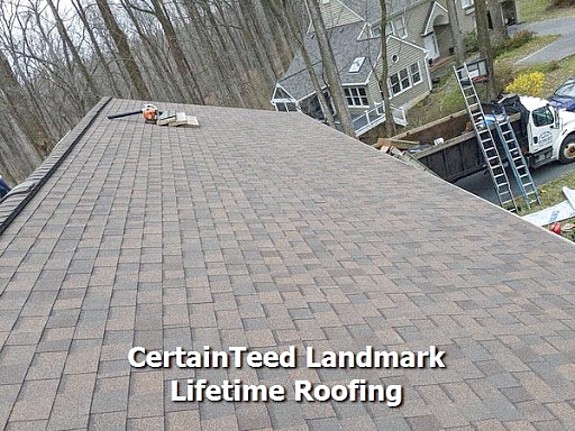
Nice 'n straight. CertainTeed has the best
colors and patterns.
|
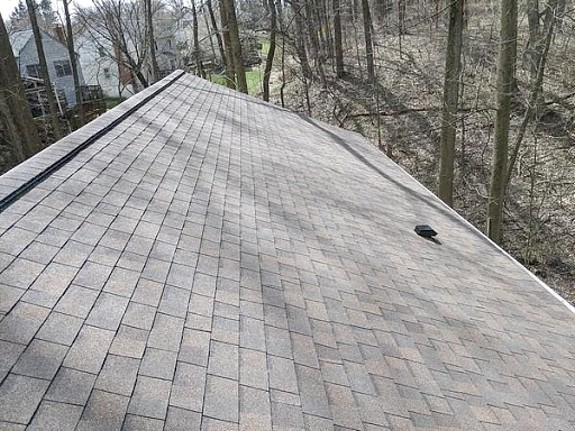
This is where all of the damage occurred. Now
it's the strongest part of the roof!
|
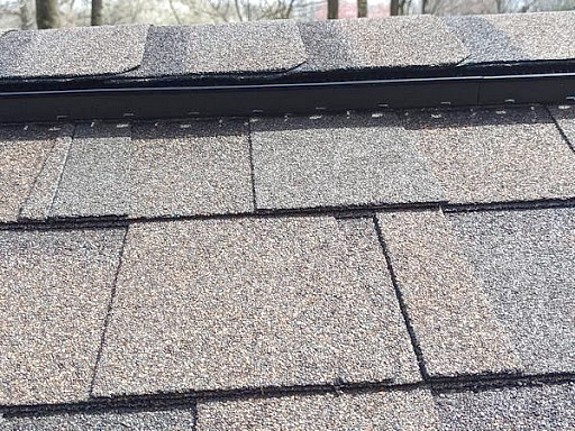
The Shingle Vent II will move way more air than the
old vent; plus we enlarged the slot a bit.
|
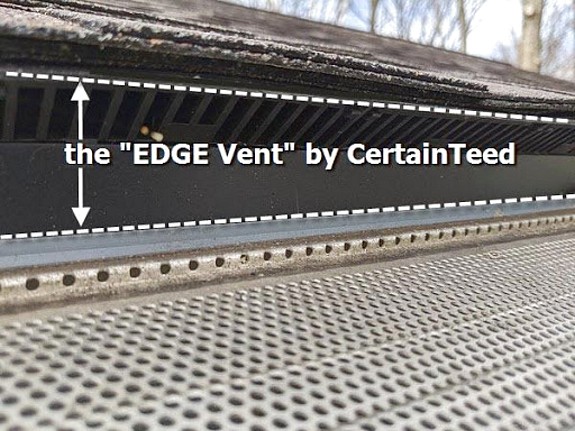
This new Edge Vent will pay for itself in energy
savings in about 3 years... AND it will remove humidity in the summer and winter without using any
power. It's the new green deal. Check out our video of an Edge Vent
Installation we did a while
back...
|
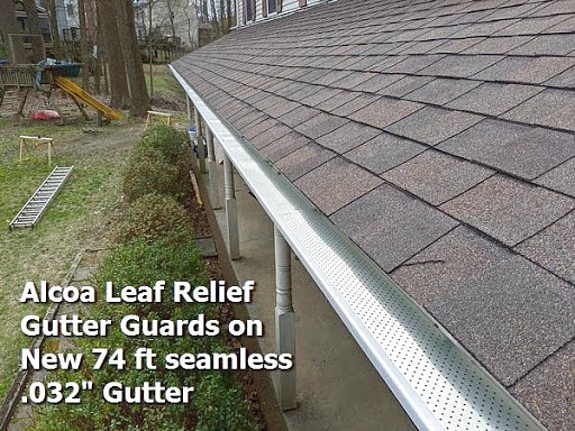
This .032" gutter with the interlocking Alcoa Leaf
Relief guards are the strongest setup on the market. |